Capacity Management
Categories: Company Management, Accounting
Think of all the things a company needs in order to produce something and make money. That's the essence of capacity management. In many industries, particularly manufacturing, they need people, office and production space, equipment, technology, raw materials and finished inventory. The bean counters want to measure how much they can potentially produce within the limits of the resources they currently have.
A donut shop might be able to make 2,000 donuts a day, a call center can handle 5,000 customer complaints in one shift, or a speaker company can make 600 woofers and tweeters a day. If a larger-than-expected order comes in, or a critical piece of equipment breaks down, the company needs to figure out how they can temporarily expand their capacity to fill the order or implement Plan B to work around the broken machine.
The last thing they want to have happen is to run out of a product and be unable to meet customer demand. Then they risk losing them for good to the competition. On the other hand, if a company is operating at 100% capacity, they risk wearing out their equipment or exhausting their employees. Excess capacity is also a no-no as that will affect the company's balance sheet. Perhaps they have unused office space, too many employees or too much finished inventory that is tying up their cash.
So, capacity management is a delicate balancing act that only the brave take on.
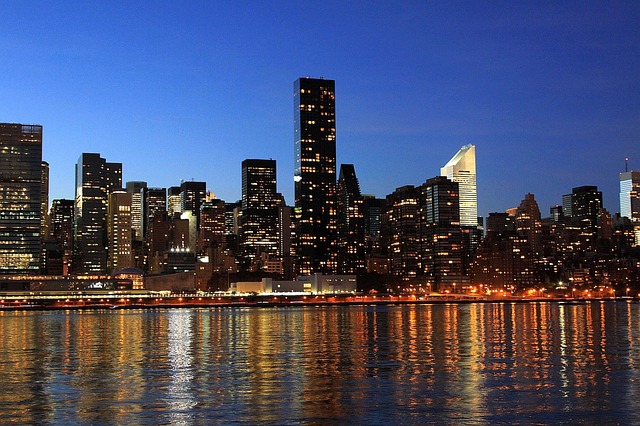